Multiskalige Geometrieprüfung von Fügezonen (SFB 1153 C5)

Leitung: | PD Dr.-Ing. Dipl.-Phys. Markus Kästner; Dr.-Ing. Lennart Hinz |
E-Mail: | pascal.kern@imr.uni-hannover.de |
Team: | Pascal Kern, M. Sc. |
Jahr: | 2015 |
Förderung: | DFG |
Laufzeit: | 2015-2027 |
Weitere Informationen | https://www.imr.uni-hannover.de/de/forschung/forschungsprojekte/forschungsprojekte-detailansicht/projects/multiskalige-geometriepruefung-sfb-1153-c5 |
Sonderforschungsbereich 1153 – Prozesskette zur Herstellung hybrider Hochleistungsbauteile durch Tailored Forming - C5 - Multiskalige Geometrieprüfung
Forschungsschwerpunkt des Teilprojekts C5 ist die flächige 3D-Geometrie-Rekonstruktion schmiedewarmer Tailored-Forming-Bauteile unter Nutzung optischer Triangulationssensoren. Die Prüfung der geometrischen Merkmale der Fügezone nach jedem einzelnen Prozessschritt ermöglicht die Einstellung des Herstellungsprozesses, eine Fehlerfrüherkennung, wie auch die Evaluierung von Bauteilverzügen, die durch inhomogene Abkühlprozesse der hybriden Materialpaarungen entstehen können.
Video
MOTIVATION UND ZIELSETZUNG
Es werden unterschiedliche Sensorkonzepte unter Nutzung aktorbasierter und algorithmischer Kompensationsverfahren für den Lichtablenkungseffekt im wärmeinduzierten inhomogenen Brechungsindexfeld erforscht.
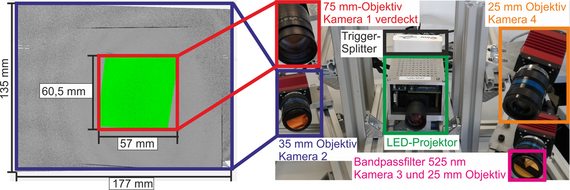
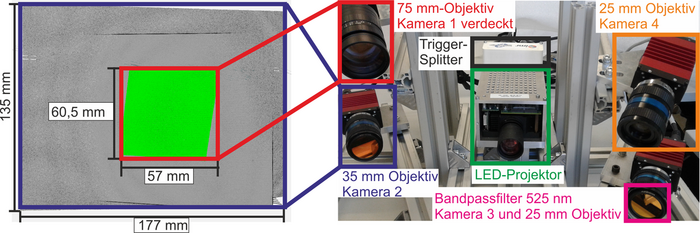
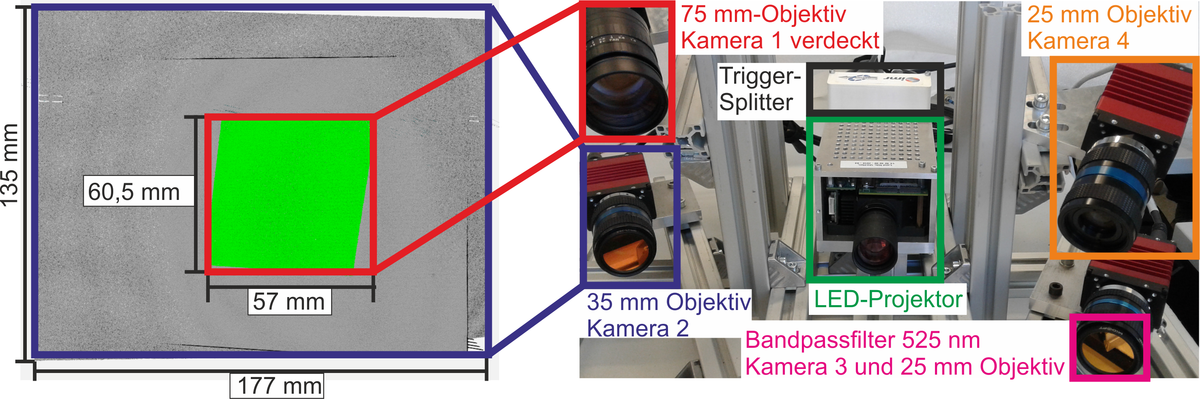
Zur Realisierung einer algorithmisch kompensierten Geometriemessung wird ein Multikamera-Streifenprojektionssensor entwickelt (Abb. 1). Dieser ermöglicht eine redundante Geometriedatenakquise überlappender Messbereiche auf Basis unterschiedlicher Triangulationswinkel. Dabei bilden alle Kamera-Projektor-Kombinationen sogenannte Stereopaar-Messeinheiten, mithilfe derer 3D-Geometriedaten akquiriert werden können. Durch die Analyse der unterschiedlich stark vom Lichtablenkungseffekt beeinflussten Stereopaar-Messergebnisse und auf Basis von Brechungsindexfeld-Simulationen kann eine algorithmische Messwertkorrektur für zylindrische Bauteile realisiert werden. Mithilfe der Finite Elemente (FE)-Simulationssoftware Comsol wurde außerdem ein numerisches Modell implementiert, das den multiphysikalischen Zusammenhang zwischen der hitzeinduzierten Dichtereduzierung der Luft und dem dadurch entstehenden Lichtablenkungseffekt abbildet, und virtuelle Triangulationsmessungen unter optischer Inhomogenität ermöglicht (Abb. 2).
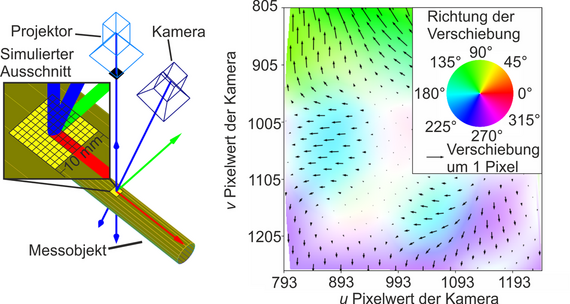
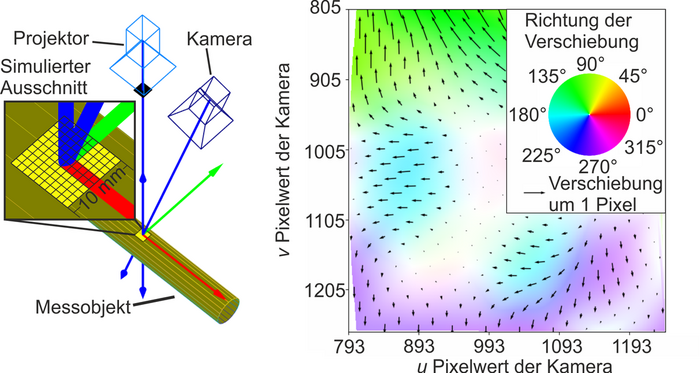
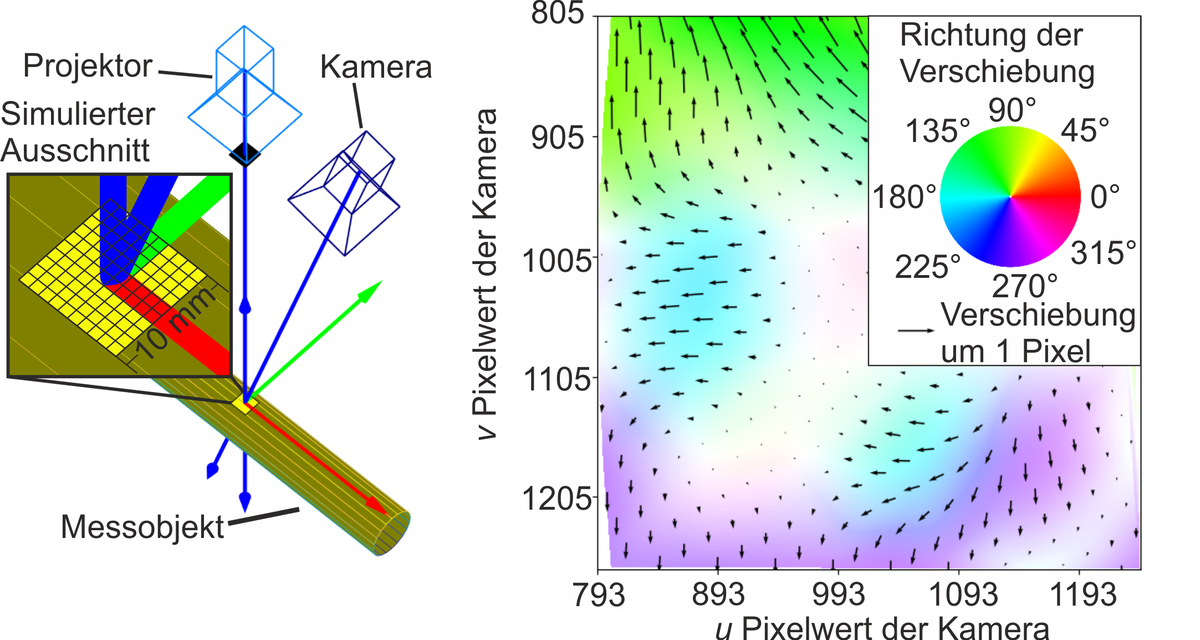
AKTUELLE ARBEITEN UND AUSBLICK
Zur experimentellen Validierung der algorithmischen Messwertkorrektur und zur Durchführung von Schrumpfungs- bzw. Verzugsmessungen direkt nach dem Umformprozess wird ein Messkammer-Sensorkonzept erforscht, das durch Druckreduktion eine Geometriecharakterisierung heißer Tailored-Forming-Bauteile mit vernachlässigbarem Brechungsindexfeld-Einfluss ermöglichen soll. Der Unterdruckansatz wurde zunächst mithilfe von Brechungsindexmessungen mittels der zweidimensionalen (2D) background oriented schlieren (BOS)-Methode validiert. In Abb. 3 ist der Prüfstand mit Unterdruckkammer dargestellt. Das sich einstellende Brechungsindexfeld über einem heißen Messstab (circa 1000 °C) innerhalb der Kammer bei Umgebungsdruck (p=987 mbar) und bei reduziertem Kammerdruck (circa 64 mbar) ist auf der rechten Seite dargestellt. Es zeigt sich, dass eine Druckreduktion die Variation des Brechungsindexes in Luft deutlich verringert. Die Beschickung der Unterdruckkammer, ein rot-glühender Messzylinder in der Kammer und der Sensorkopf zur Durchführung von Geometriemessungen durch das Kammermessfenster sind in Abb. 4 dargestellt.
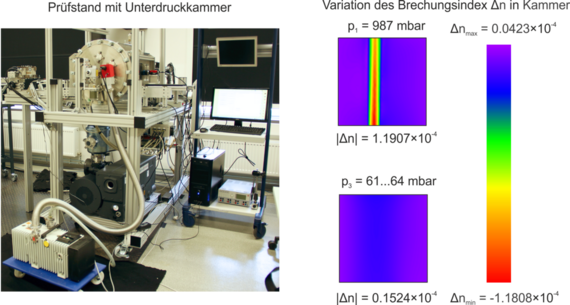
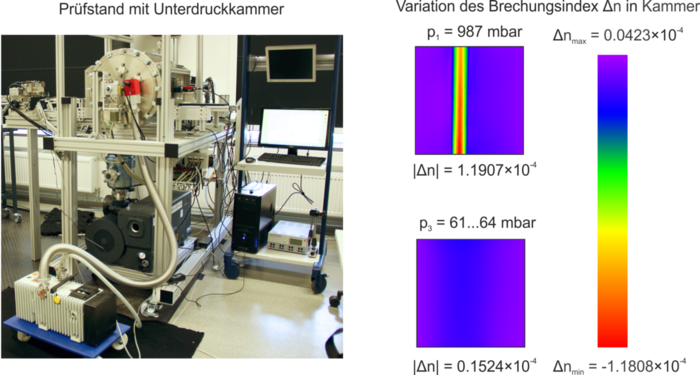
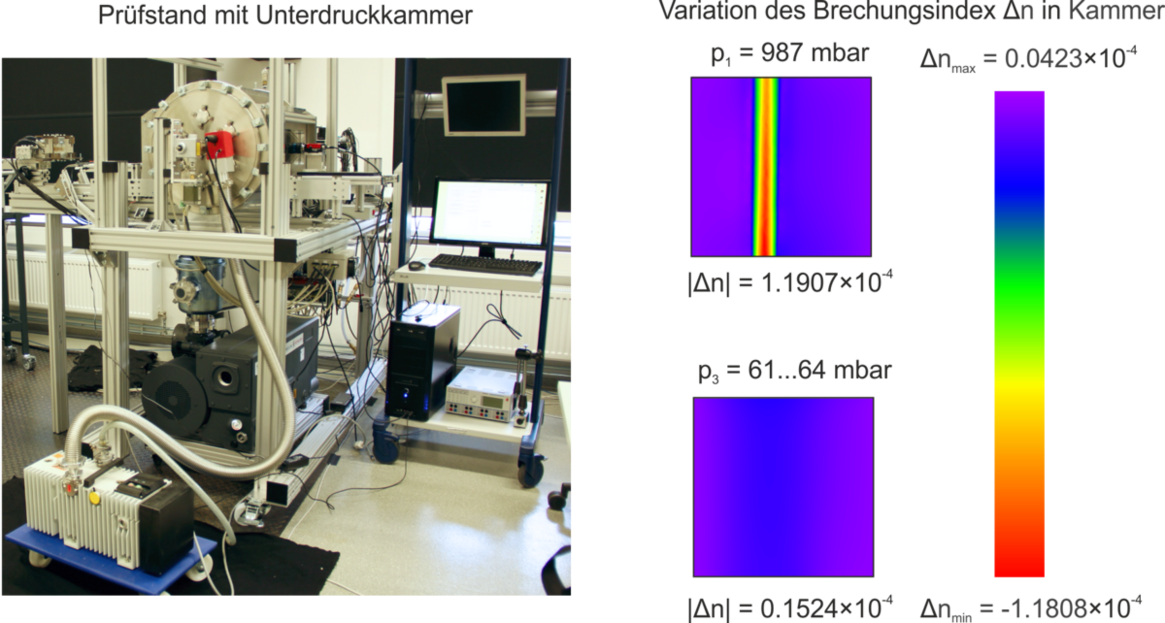
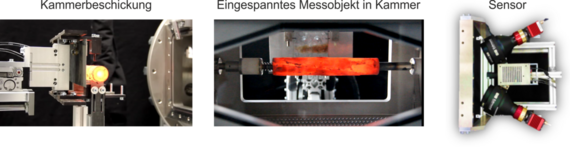
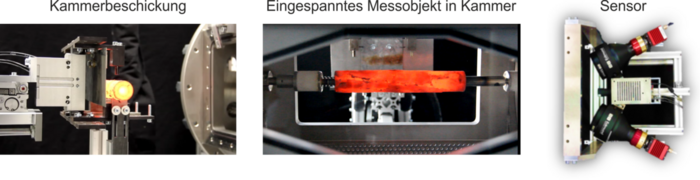
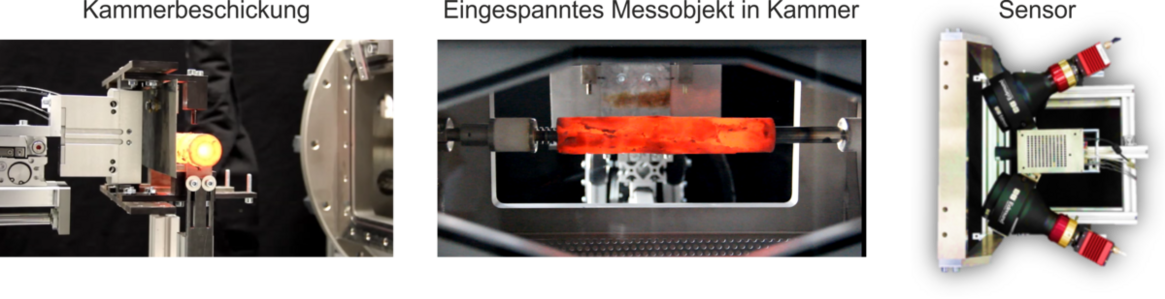
Zur umfangreichen Charakterisierung von Schmiedeprozessen ist es zudem geplant, eine Themographiekamera mit einem Triangulationssensor zu koppeln. Dies ermöglicht eine Zuordnung von experimentell ermittelten Temperatur- und Geometriedaten (4D-Modell des Messobjektes, Abb. 5). Durch Vergleich von Umformsimulationen und Messdaten lässt sich eine Validierung der Simulationen erreichen.
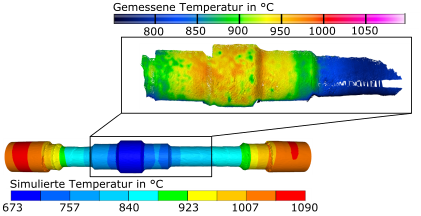
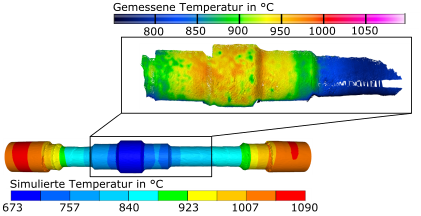
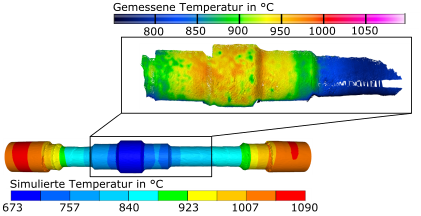